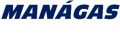
Complete Guide to Gas Mixers and its various applications
Complete Guide - MIG MAG Welding (GMAW) - Shielding Gases
Choosing the appropriate shielding gas for MIG MAG welding can greatly improve the quality of the weld, in addition to saving time and money. To choose the appropriate gas or mixture, you must consider several factors, including the material, the transfer method, the cost and the amount of cleaning required.
After all, what gas is used for MIG MAG welding? Usually, as a shielding gas, an inert gas is used for MIG MAG welding. The shielding gas prevents unwanted contaminants such as oxygen and nitrogen, present in atmospheric air, from entering the welding area.
Shielding gas mixtures are often used in welding processes, being composed of inert gases and/or active gases. In addition, active gases are also used in small percentages, which, and technically transforms the MIG process, into a MAG or GMAW welding process.
For ferrous or non-ferrous metals, the options for shielding gases are mixtures of Argon and Carbon Dioxide, or both pure gases. There are also gas mixtures specific for steel welding. On the other hand, the inadequate choice of shielding gases for a given welding process generates oxidation marks on the part, inconsistent bead patterns, excessive smoke and spatter.
There are several options for welding gas mixtures and the choice may seem difficult at first. However, in this post, we will describe the best options for MIG MAG welding based on several different applications.
TABLE OF CONTENTS:
1. Inert Gases – Argon and Helium

An inert gas, or a noble gas, is a gas that is highly resistant to chemical changes in certain circumstances. Argon and helium are the two inert gases used in MIG and TIG welding. Argon is the inert gas most commonly used for MIG welding, either alone or mixed with one or two other gases. Argon leads to shallow weld penetration, but with a wider bead, and to a stable arc, while helium transfers more heat to the part than argon and is more expensive.
Argon and helium tend to be mixed with other gases, as both are expensive. In addition, mixtures composed only of inert gases such as argon and helium are normally limited to use in non-ferrous metals such as aluminum and copper. Since inert gases are resistant to a chemical reaction, they result in less spatter than active gases. Another consideration is that, although helium reduces the porosity of the weld, it also uses more energy and more caution should be exercised to prevent burns and overheating.
2. Active Gases
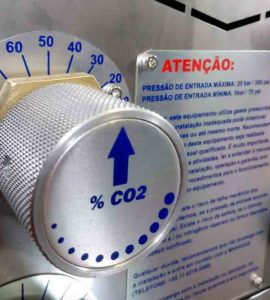
Considering welding processes, an active gas is also resistant to chemical changes, but to a lesser extent than inert gases. Carbon dioxide (CO2) is an active gas, which is often used in MAG welding, either pure or mixed in small percentages with an inert gas. The main advantages of CO2 are that it is cheaper than inert gas and allows a deeper penetration of the metal. The main disadvantage of CO2 is that its arc characteristics are more severe and result in more spatter, which, in turn, will require more cleaning around the weld.
Oxygen is a non-inert gas that is used in very small percentages to increase weld penetration in thicker metals and stainless steel. This sounds counter intuitive, as oxygen is also responsible for the oxidation and rust found in defective welds. However, in very small percentages (one to five percent), it helps to stabilize the arc and is cheaper than helium.
3. C25 Gas Mixture Advantages, and Argon and CO2 gas mixtures
Argon and carbon dioxide, with their various properties present advantages and disadvantages and several mixtures combined both gases have been developed in order to meet certain demands. One of the most common gas mixtures for MIG welding is a mixture of 75% argon to 25% carbon dioxide known as C25. Mixtures of 80% argon and 20% CO2, as well as 90% argon and 10% CO2 are also common.
On the one hand, welding with the C25 mixture can be more costly than welding with 100% pure CO2. On the other hand, welding with a C25 mixture is cheaper than welding with pure argon. The higher the argon content, the higher the cost of the gas mixture. At the same time, the welding profile of the C25 is much narrower and results in less spatter and cleaning than 100% CO2. For most MIG welding applications, the C25 mixture is ideal and to offset the cost, when compared to pure CO2, the adoption of a gas mixer can compensate for the investment.
While the C25 mixture is the most common option, the welding transfer method will also determine the concentrations of Argon and CO2 used. Gas mixtures for protection with 25% or more carbon dioxide content are more suitable for short-circuit welding. Higher levels of argon are better for globular transfer and spray arc welding as they help to limit spatter. Again, the big drawback here is the cost.
4. The Ideal Gas for Welding Carbon Steel
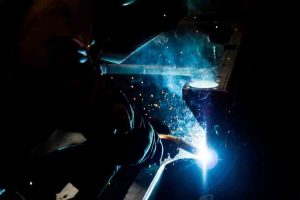
Mixing C25 and welding with 100% CO2 are the most commonly used options for carbon steel. For carbon steel, we also recommend ternary mixtures containing argon, carbon dioxide and oxygen Mild steel, or low carbon steel, is easier to weld or machine and is more affordable than high carbon steel. The low carbon content of mild steel and the lower levels of other metal alloys, in addition to making it more accessible, also make it more prone to oxidation and rust.
Mixtures of shielding gases composed only of inert gases, such as argon, are not suitable for MIG MAG welding and carbon steel, as it results in an irregular and inconsistent bead. The appearance of the cord is also impaired.
Argon mixtures containing one to five percent oxygen are common for industrial applications, such as in the automotive, carbon steel and stainless steel industries. The risk of oxidation and rust of these oxygen-containing mixtures increases for mild steel with lower carbon content.
5. Ternary Gas Mixtures and Stainless steel
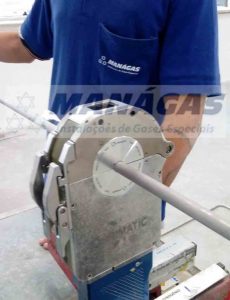
For stainless steel, there is also the option of adopting ternary gas mixtures containing helium, argon and carbon dioxide or helium, argon and oxygen. An example is the mixture of ternary gases with 90% helium, 7.5% argon and 2.5% CO2. Again, additional levels of helium transfer more heat to the part, while oxygen helps to increase penetration into thicker metals and stabilize the arc. Both CO2 and helium require higher voltages to sustain a stable arc, with helium being the most expensive of inert gases. A more accessible and common option for stainless steel is the mixture of C2 gases, composed of 98% argon to 2% carbon dioxide.
Although mixtures of ternary gases have several benefits, they can also have a high cost. The solution to reduce the cost of mixing gas for welding and taking advantage of these benefits is to invest in gas mixers for three gases.
6. MIG x TIG Welding– Can I work with the same gas mixture?
TIG welding, or welding with tungsten inert gas, is another form of welding that uses an inert gas; however, TIG welding uses only inert gas. Also called GTAW (tungsten gas arc welding), TIG welding depends only on argon, helium or a mixture of the two. Although it is technically possible to weld with mixtures containing gases such as carbon dioxide or oxygen, this procedure is not recommended. Carbon dioxide will lead to outbreaks, interruptions and overheating.
Since TIG welding requires 100% inert gas, we can use 100% argon for TIG welding. For MIG welding on thin aluminum (less than ½”) we can also use Argon. However, for most other MIG welding applications, especially for steel, 100% argon gas is not recommended.
Therefore, if the welder makes many TIG and MIG welds, the ideal scenario is to work with an Argon and Carbon Dioxide gas mixer. In this way, depending on the welding process, MIG or TIG, and the material (aluminum, carbon steel, stainless steel, …) the welder can easily adjust the gas concentrations in order to obtain the ideal weld bead and meet a wide range of applications.
7. MIG Welding – Pressure
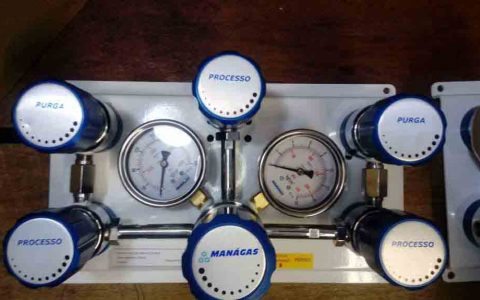
For most pressure regulators for welding process, the outlet pressure is set in psi or in some cases in bar or kPa is regulated from a minimum of 25 psi (1.7 bar – 170 kPa) to 80 psi (5.5 bar – 550 kPa). Regulators designed for CO2 generally range from 50 to 80 PSI. On the way to the hose with the welding torch, this pressure is reduced again through a needle valve with an internal diameter of 0.5 to 0.7 mm, resulting in a welding pressure of 3 psi (0.2 bar) at 8 psi (0.55 bar). Welding working pressure depends on internal torch tip constraints caused by spatter or gun cable constraints.
8. MIG Welding – Flow rate
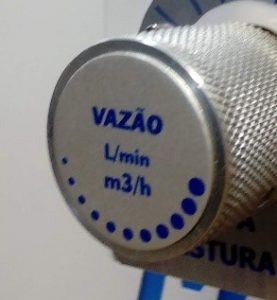
While the gas pressure represents the force exerted by it in a given area, the gas flow represents the amount of gas in volume (measured in cubic feet or cubic meters) present in a flow per unit of time, for example hour. So, in the case of flow in cubic blades per hour, we have the CFH unit. If the flow unit is in cubic meters per hour, we have m3/h.
For the MIG MAG welding process, the gas flow or flow rate needs to be high enough to protect the weld, but a setting too high can actually draw air into the weld and “attract” contamination to the melt pool, according to the figure below:
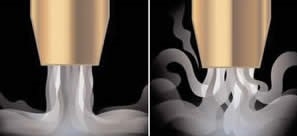
While in an enclosed area, the setting can be as low as 15 CFH (cubic feet per hour) or 0.4 m3/h, although depending on the welding pass, the shielding gas flow can reach up to 50 CFH (1, 4 m3/h). The proper gas flow also varies based on the nozzle diameter. Always check the manufacturer’s recommendations for your welding equipment.
To define the shielding gas flow, other factors must be taken into account, such as the surface and welding speed. Welding flat surfaces requires a higher gas flow than welding grooved materials. Fillet welds typically require the lowest flow rates as they are protected against drafts, while butt welds require a higher gas flow. Increasing your welding speed will also require a higher gas flow, as well as welding a thicker material.
9. MIG Welding – defining the most suitable gas mixture
For MIG weld protection, probably the best gas mixture, with the widest application, is 75% Argon and 25% CO2. Mixtures with 80% Argon and 20% CO2 can also be a good option. If the final application is professional, where performance, speed / productivity, no splashing is important, we recommend the flexibility that a gas mixer provides. Depending on the gas mixer model, mixtures can be carried out directly from the pure gas cylinders (PORTABLE MODEL gas mixer).
If the welder is on a limited budget and doesn’t mind cleaning up a little extra spatter, carbon dioxide is cheap and great for welding or hobby experimentation. For aluminum MIG welding or TIG welding in general, 100% argon is always the best alternative.
For stainless steel welding, the ideal is to work with mixtures of ternary gases of Helium, Argon and CO2 or Oxygen. Alternatively, mixing C2 gases is inexpensive.
It is very important to always consider which materials will be welded, pressure and flow of work and determine the ideal gas or gas mixture to obtain a consistent bead pattern and to avoid overheating the material.
QUESTIONS related to “Complete Guide – MIG MAG Welding (GMAW) – Shielding Gases”
Any questions and comments related to “Complete Guide – MIG MAG Welding (GMAW) – Shielding gases?”, please feel free contact us at any time. In addition, please take this opportunity to explore our product line of high performance gas mixers for MIG MAG welding (GMAW welding).
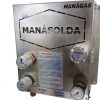
Gas mixer designed and manufactured for the welding process, which allows mixing between 02 gases, with flow rate and outlet pressure control. From 0 to 100% content adjustable gas mixing output.
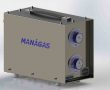
Compact gas mixer designed and manufactured for the welding process, which allows mixing between 02 gases, with outlet flow rate control. From 0 to 100% content adjustable gas mixing output. Requires cylinder/first stage pressure regulators for both input gases.