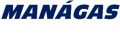
Complete Guide to Gas Mixers and its various applications
Welding Processes - Plasma Cutting and Shielding Gases
Please find below, some common questions and respective answers regarding the welding, plasma cutting and shielding gases or gas mixtures.
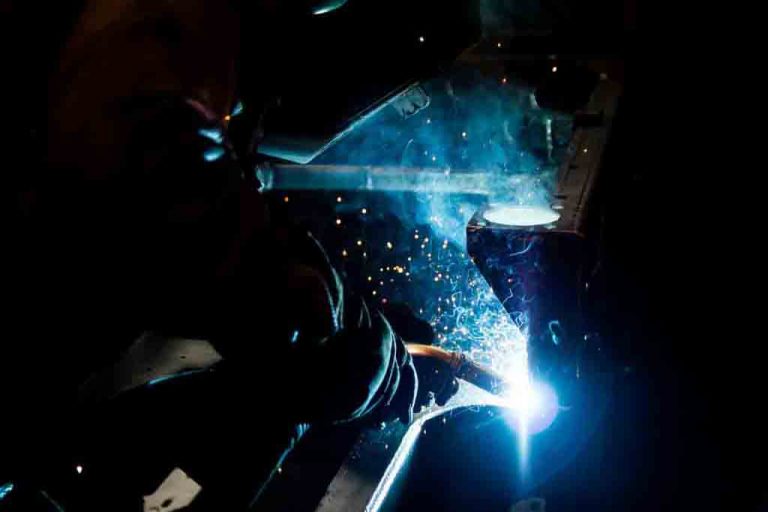
Table of Contents:
1. What is the best gas or gas mixture to MIG MAG (GMAW) weld?
For MIG welding, use Argon (Ar) or Helium (He) as the welding gas. MIG welding is suitable for non-ferrous materials such as aluminum, copper, bronze and their alloys.
For MAG welding, use Carbon Dioxide (CO2) or gas mixtures for the welding gas. Note that, MAG welding requires an active gas, where there is interaction with the melt pool. MAG welding is suitable for ferrous metals.
2. Considering the MIG and MAG welding processes, what is the difference between the welding gases?
Argon (Ar) – Inert gas. Argon for MIG welding or MAG welding can contribute in both processes, pure or in combinations/mixtures with other gases to optimize the electrical arc formations, necessary for the welding of ferrous and non-ferrous metals. For MIG welding process, suitable for aluminum and bronze in filling operations.
Helium (He) – Inert Gas. In MIG welding, suitable for wider weld beads, less depth, more productivity due to the higher welding speed (compared to argon). Helium has a higher thermal conductivity, transferring more heat to the part and making the weld bead more “fluid”. In relation to Argon, Helium has a higher cost.
Carbon Dioxide (CO2) – Active Gas. In the welding process MAG protects the material being welded, as it does not allow an extreme temperature increase and, thus, preserves its mechanical properties and still generates a weld bead with greater depth and mechanical resistance. As a single welding gas, CO2 forms a turbulent arc and causes a lot of splash.
Welding Gases - MIG MAG Welding Gas Mixture
Gas mixture combining Argon (Ar) – Inert and Carbon Dioxide (CO2) – Active. Ideal, as it generates better looking weld bead and less splash. It is common to have low penetration in the weld region, but as the Argon concentration increases in the gas mixture, it also increases the depth of the bead. The content of Argon in the welding gas mixture can be between 60 to 80%.
3. For TIG welding, what is the best gas?
For TIG welding, the most common welding gas is Argon. However, in order to maximize quality and productivity, there are options of gas mixtures combining Argon and Helium and Argon and Hydrogen.
4. For plasma cutting, what is the ideal gas or gas mixture? Argon-Hydrogen, Nitrogen, Oxygen or Compressed Air for Plasma Cutting?
For plasma cutting, an active or inert, ionized gas is used as an atmosphere for the electrical conduction of the plasma, which will be used under the piece of carbon steel, stainless steel or aluminum that will be cut.
The plasma, electrically conducting atmosphere, can also be formed by gas mixtures and the choice of these gases depends on the thickness of the piece, quality and speed of the plasma cut.
Compressed Air – needs to be treated to remove particles, but it has low cost and high availability and can be used for plasma cutting of carbon steel, stainless steel and aluminum.
Oxygen – mainly indicated for plasma cutting of carbon steel.
Nitrogen – for plasma cutting of stainless steel and aluminum, Nitrogen has high consumable yield, quality and cutting speed.
Argon/Hydrogen mixture – indicated to maximize machine performance and plasma cutting of thicknesses over ½ inch for stainless steel and thick aluminum.
5. Considering welding gases, what are the advantages of adding small concentrations of Oxygen to Argon?
6. Advantages of Argon and Oxygen Gas Mixtures:
Welding gas – Argon/1% Oxygen mixture is used to:
a) Used for aerosol transfer in stainless steel;
b) Better arch stabilization;
c) Best drip rate;
d) Better appearance of the weld bead.
Welding gas – Argon/2% Oxygen mixture is used to:
a) Used for aerosol transfer in carbon steel, low alloy steel and stainless steel;
b) Better wettability than the mixture with 1% oxygen;
c) There is no difference in the performance of the mechanical properties and corrosion of welds made with 1 or 2% oxygen.
Welding gas – Argon/5% Oxygen mixture is used to:
a) Ideal for carbon steel;
b) More fluid fusion pool;
c) Enables increased speed and welding, more productivity.
Welding gas – Argon mixture/8% to 12% Oxygen is used to:
a) For single-pass welding;
b) To define the chemical composition of the welding wire, consider a high oxidation potential of the mixture;
c) For transfer by spray or aerosol, it has a lower transition current and greater fluidity from the fusion pool.
Welding gas – Argon mixture/12% to 25% Oxygen is used to:
a) Restricted use, therefore, the advantages and benefits are questionable when compared to the mixture of 8 to 12% of Oxygen;
b) Excessive fluidity of the fusion pool;
c) Thick layer of slag on the surface of the weld bead with difficult removal;
d) In the mixture of 25% Oxygen in Argon, complete welds with reduced porosity formation.
7. Advantages of Argon and Carbon Dioxide Gas Mixtures:
Intended for welding carbon steel, low alloy steel and in some cases stainless steel. The mixture of Argon and Carbon Dioxide reduces the splash rate. A low concentration of Carbon Dioxide in the mixture with Argon makes the aerosol transfer similar to the mixture with small levels of Oxygen.
In the case of mixing with carbon dioxide, the transition currents have higher values. Slightly higher currents must be achieved with the addition of CO2 in the mixture for the MIG MAG welding process, in order to stabilize the aerosolized metal transfer through the electric arc.
In aerosol transfer, the addition of Oxygen reduces the transition current. In the mixture of gases in combination with Argon and above 20% of Carbon Dioxide, the process presents instability in the aerosol transfer and the transfers become short-circuited and/or globular.
Welding gas – Argon mixture/3 to 10% carbon dioxide is used to:
a) Used in carbon steel with transfer by short circuit and aerosol;
b) Mixing Argon with 5% Carbon Dioxide is ideal for thick pieces of low alloy steel in pulsed MIG welding process out of position;
c) Less oxidation compared to the 98% Argon/2% Carbon Dioxide mixture;
d) When replacing Oxygen with Carbon Dioxide in welding mixtures, it is possible to obtain greater penetrations and less porosity;
e) In terms of wettability, when compared to welding mixtures containing oxygen, it will be necessary to double the concentration of carbon dioxide to achieve the same effect.
f) With carbon dioxide concentrations between 5 to 10%, the arc becomes defined and strong, making the melt pool much easier to control.
QUESTIONS:
Any questions and comments related to the topics covered above, please feel free contact us at any time. In addition, please take this opportunity to explore our product line of high performance gas mixers for Plasma Cutting.
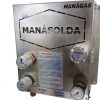
Gas mixer designed and manufactured for the welding process, which allows mixing between 02 gases, with flow rate and outlet pressure control. From 0 to 100% content adjustable gas mixing output.
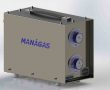
Compact gas mixer designed and manufactured for the welding process, which allows mixing between 02 gases, with outlet flow rate control. From 0 to 100% content adjustable gas mixing output. Requires cylinder/first stage pressure regulators for both input gases.